Related keywords recommendation: high frequency heating equipment
When the press slide is reversed, the finished part moves up with the female block and platen. The platen stops at the level of the punch, while the female module continues to move with the upper platen.
The anti-wedge block installed on the upper formwork interacts with the journal of the pressure plate, and retracts the pressure plate and the concave module connected to its pin to the position limited by the stopper. Grooved section parts are traditionally manufactured in a dedicated die with 1 or 2 punches. It can also be punched in units with a universal tool, however, the flat section 3 should be sufficiently wide for this method.
When manufacturing the punch and die of the special mold, it should be entered from the nominal thickness of the material. Set off to match the work surface. In the closed position, the mold should correct the flat segment of the part and exclude the effects of free bending of the blank.
The actual value of stock thickness in may differ from in. Values vary widely, so not all segments are subject to correction. The uneven correction effect will negatively reflect on the accuracy of the part, which is one of the disadvantages of the traditional process. The disadvantage of the traditional process is also the high cost of tooling and equipment, because the peak load characteristics of the press generate too much power.
The pressure value of the high frequency machine on the die edge on the blank. The tensile resistance of the blank on the bent section is significantly weaker. The opposite effect is the hardening of these segments due to bending, which occurs faster than the hardening of flat segments.
When determining the minimum allowable fillet radius Rmin of punch and die, the following conditions should be considered, that is, the blank section that is not in contact with the mold should be transferred into a plastic tensile state before the bearing capacity of the blank section subjected to contact pressure disappears.
The obtained value Rmin is nearly 50% larger than that of general bending. For low carbon steel, the Rmin value does not exceed the thickness of the material. The limit angle of the inclined wall was nearly 45° when testing the specimen, which was confirmed by the results of the test stamping section.
When measuring the straightness of the part's sloping busbar, it was found that there is a deviation, but it does not exceed the thickness tolerance of the blank material. At this time, the stretch deformation of the busbar is within 10%, and the stretched section extends along the width, that is, the length direction of the profile is less than 2mm.
During stretch bending, the edges of the blank are moved towards the punch, preferably these movements are carried out with the die, otherwise the segment will slide along the edge of the die and undergo bending and subsequent straightening, causing excessive deformation of the segment Thin. A mold structure with movable concave modules was developed, and the mold was mounted on a press with a high-power buffer for clamping the edge of the blank.
The working process of the mold is as follows: the blank is placed on the punch and the platen. The pressing plate is installed in the guide groove of the movable plate. When the upper platen goes down, the concave module installed in its guide groove presses the edge of the blank on the pressing plate and moves with the stroke of the slider of the press, which overcomes the back pressure of the buffer ejector rod.
The blank is then bent around the edge of the die, causing tension within the blank to move the die block and platen perpendicular to the stroke of the press slide. When the bending angle of the blank reaches the desired value, the platen and the wedge start to interact.
The planes they contact also have an equal inclination angle, so that the resultant movement direction of the pressure plate is along the wall of the curved part. The edge of the blank, clamped by the friction between the female module and the pressure plate, moves with the pressure plate.
When the press slide is reversed, the finished part moves up with the female block and platen. The platen stops at the level of the punch, while the female module continues to move with the upper platen. The anti-wedge block installed on the upper template interacts with the journal of the pressure plate and retracts the pressure plate and the concave module connected to its pin to the position limited by the stopper
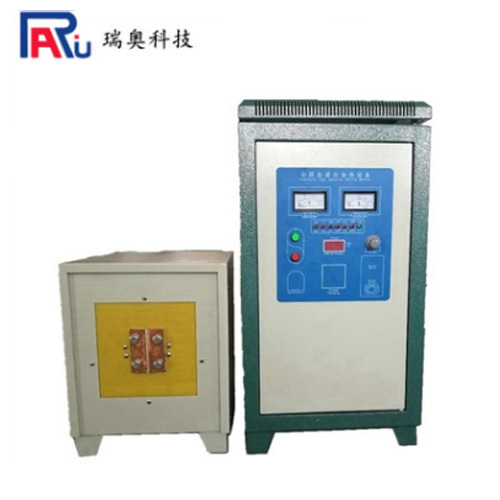